In the food and beverage industry, safety is paramount, and providing consumers with a consistent product experience can protect your brand. The complexity of food production processes involves the risk of contamination by metal, glass, or other substances. Foreign body inspection is critical to ensuring the quality and integrity of your final products, and may be required by specific customers or local or regional guidelines. Finding and removing physical contaminants also protects your valuable processing equipment and can help ensure a smooth and uninterrupted production process. But which inspection method is best for your operations?
Is Metal Detection or X-ray Inspection Better for My Application?
Both metal detection and X-ray inspection can help ensure quality and protect your equipment and the consumer, but each technology has different strengths and is better suited to specific applications. Before choosing a foreign body inspection method for your operations, consider the materials you will be inspecting, what physical contaminants or defects you are most concerned with, and where in your production process inspection can be most effective. Let’s start by taking a look at the basics.
Characteristic | Metal Detection | X-ray Inspection |
What is detectable? | Ferrous and non-ferrous metals only | Metals, glass, ceramics, calcified bones, some plastics |
Technology | Senses metal by disturbances in balanced electromagnetic field | Discerns contaminants from density differential |
Product Effect | Possible significant impact in sensitivity due to variation in product temperature, packaging, and product make-up. | Generally not affected by product temperature variations. Sometimes limited by thickness variations or very high densities. |
Other Capabilities | Generally only detects physical contaminants | Can detect product anomalies, such as missing and broken items |
Packaging that contains metal (metallized film, aluminum foil, tin cans, etc.) | Cannot detect inside metal packaging, except some metallized films, with limitations | Can detect inside metal packaging |
Price | Typically less expensive option | More cost and more maintenance |
Longevity | Typically 10 – 20 years | Typically 5 – 10 years |
1.) What are you inspecting?
Because materials behave differently under different types of foreign body inspection, the product you are processing can help determine which technology is more appropriate for your operation. Metal detectors operate by sensing a disturbance in a balanced electromagnetic field to confirm the presence of contaminants, so certain product attributes (like salt or iron content, moisture, and temperature) can interfere with the results. X-ray identifies materials by their relative density and the application of proprietary software algorithms, which then show up as various shades of gray on an X-ray image. The orientation of a contaminant, its shape and thickness, and packaging material can all affect how clearly it can be seen.
2.) What physical contaminants are you most concerned with?
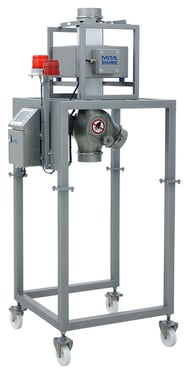
Physical contaminants can arise anywhere in the production process, and may be glass, ceramic, stone, or metal fragments. They may also originate outside the production plant, such as debris from the field or broken pieces of farming or harvesting machinery.
If you anticipate finding glass, ceramic, or certain bones (such as uncooked, calcified bones), X-ray is the right choice. If a container has a foil lid or inner seal, or if your packaging includes metallized film or a metal tray, X-ray is a must. X-ray is the same or better when finding ferrous and most non-ferrous metals, and is particularly good at detecting stainless steel, but not as good at aluminum detection because of aluminum’s low density. Aluminum is highly conductive, though, so it is easily detected in a conventional metal detector.
You may be concerned with plastics or other synthetic products such as polyethylene, polypropylene, nylon, or UHMW. X-ray yields somewhat limited success in detecting larger pieces of dense plastics. Some plastics used in manufacturing, such as modular conveyor components, are embedded with materials to make them more detectable in both X-ray and conventional metal detection equipment, however most synthetic materials will be missed by most detection equipment.
3.) Where in your production process can inspection be most effective?
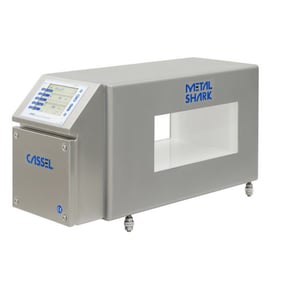
The main purpose of metal detectors is consumer protection, but protecting your production machinery is also an important benefit. Inspecting incoming raw materials offers an advantage by sorting metal contaminants out before they are crushed by processing equipment to a size that is more difficult to detect. Metal contaminants can cause severe damage to production machinery, even bringing them to a standstill, resulting in repair costs and even lost sales.
X-rays are very useful as a final quality check, as they can scan inside packaging to reveal broken products, incomplete fill levels or missing items, as well as physical contaminants like rocks, metal, or glass. X-ray can also be beneficial when inspecting products that can have a high product effect with metal detection, such as products with a high salt or moisture content.
Integrating metal detection at the point where raw materials enter the production line and either X-ray or additional metal detection after final packaging can offer more complete protection, for both your equipment and your consumer.
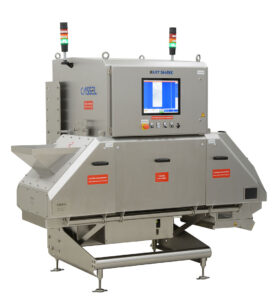
Consider a facility that processes and packages tree nuts, such as almonds. The crop is harvested and transported to your facility for processing. The first step is to detect and remove metal, which may come from harvesting machinery, transportation equipment or physical contaminants from the grove: this is done by running the raw product through a gravity-fed metal detector and, in many cases, further inspecting it with a bulk X-ray machine. The almonds are then processed and packaged. Once in their final package, the nuts may be run through either a second metal detector or an X-ray machine, which can eliminate any remaining contaminants from the grove, as well as anything that may have entered the product during processing.
Inspection of food and beverage products with metal detectors and/or X-ray is a fundamental part of responsible food production. CASSEL Inspection has the expertise and equipment to provide a complete food and beverage inspection solution for your operations. Contact CASSEL to find out more about how we can help protect your customers, your product, your brand.